Nearly every neodymium magnet will be plated or coated and, as the most powerful permanent magnet available, they are used in many different applications. However, they possess physical characteristics that require them to be plated or coated in order to protect them from damage. In their raw form, neodymium magnets are quite brittle, and as a result are prone to chipping, breakage, and other types of physical damage. Another concern is that neodymium magnets (which are 65% iron by weight content) are highly vulnerable to corrosion and prone to experiencing erosion and decay if not properly coated. Fortunately, there are many coating options available for neodymium magnets that protect damage and corrosion from occurring. Types of Coatings
The type of plating or coating used on a neodymium magnet is determined based on the application and environment in which the magnet will be used. One of the most common options is nickel plating, a three-layer plating that combines a nickel layer, a copper layer, and a nickel coating. Nickel options are typically best suited for indoor use, offer excellent abrasion resistance, and are a highly cost-efficient choice. Other nickel-plating options incorporate layers of copper, nickel, gold, and chrome. For those who desire non-nickel metal plating, zinc is also available.
There are various types of non-metal coatings available for neodymium magnets, including Teflon/PTFE coatings, plastic coatings, rubber coatings, and epoxy resin coatings. These coatings are often designed for use in specific applications, and some require speciality manufacturing.
One specialist coating is Everlube, which was originally developed as a brand of dry film lubricant products specifically designed to enhance and improve the performance of critical components and meet a wide variety of industry, defence, and customer specifications for critical components. Manufactured by Curtiss Wright, the coatings are widely used by companies including Boeing, Airbus and NASA. The Everlube anti-corrosion magnet coating combats the increasingly difficult working environments for magnets and magnetic components by preventing oxidation and deterioration of high-powered permanent neodymium rare earth magnets.
When selecting the plating or coating for neodymium magnets, there are several factors to take into consideration. Reviewing the magnet application, it is important to assess:
The environment in which the magnet operates;
How well the plating or coating resists abrasion;
How the plating or coating interacts with glue;
The thickness of the plating or coating;
How well the coating protects against corrosion and wear that can be caused by environmental factors such as humidity, water, salty air, and salt water.
The price and cost efficiency of the coating;
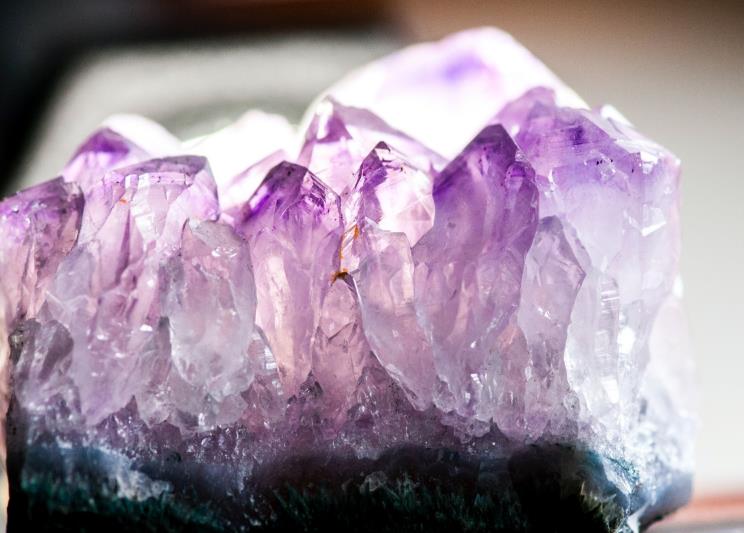
Source:https://www.bunting-berkhamsted.com/coatings-for-neodymium-magnets/